Round pipe Max. workpiece diameter | Φ152 mm |
Square pipe Max. workpiece diameter | 125 mm × 125 mm |
Max. workpiece length (loading) | 6500 mm |
Laser power | 3.0 kW |
Laser Processing Machines
FT-150 FIBER
- U-axis control provides high-speed, high-accuracy cutting
- The productivity of pipe mass production operation is automated and significantly improved
- Optional drilling and tapping can be performed by just one machine
- Reduced running costs with energy-efficient fiber laser
- New graphical user interface (GUI) of the CNC system greatly improves operability
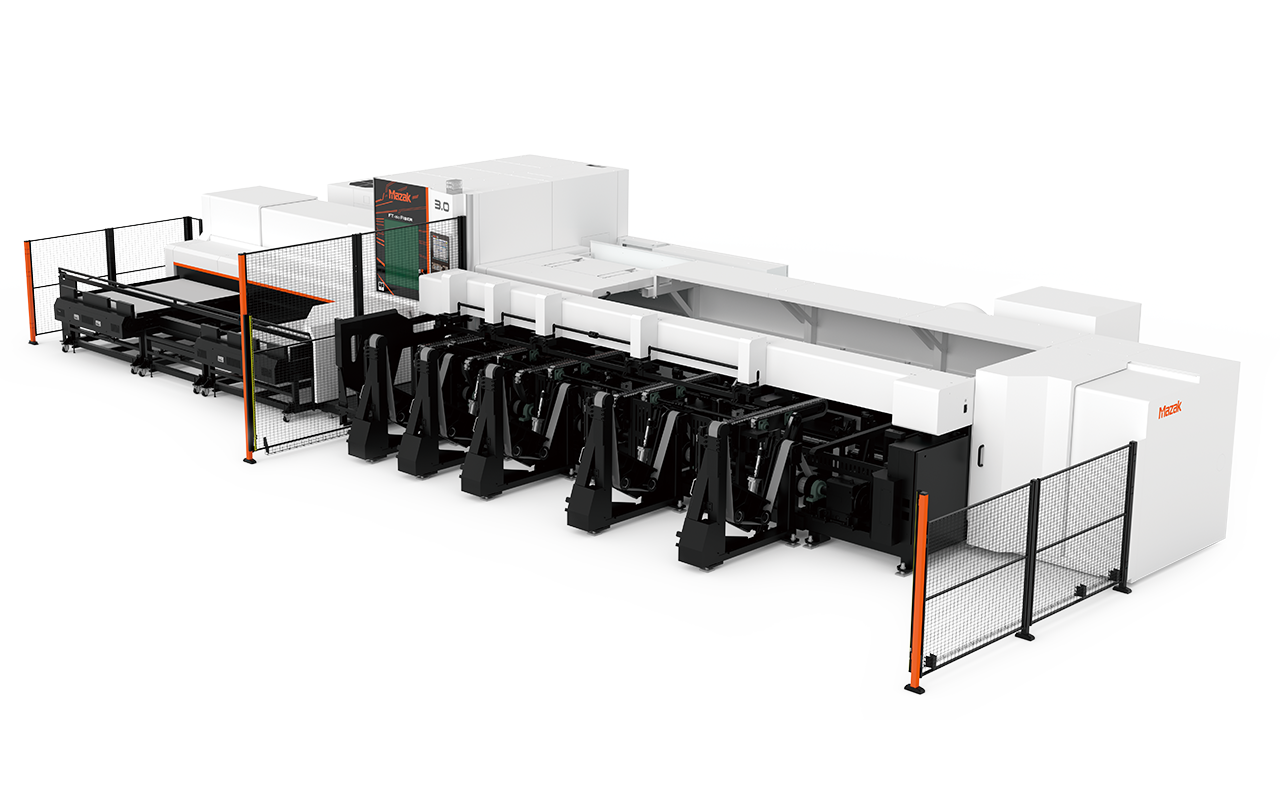
High quality and high productivity cutting of various pipes
Cutting of a variety of sizes and materials. High-speed, high-accuracy cutting by U-axis control
The FT-150 FIBER is capable of processing round pipes with a maximum diameter of Φ152 mm and square pipes with a size of 125 mm per side. The laser head can be operated at high speed by U-axis and can cut materials such as mild steel, stainless steel, copper, brass, and aluminum with high speed and high-accuracy.
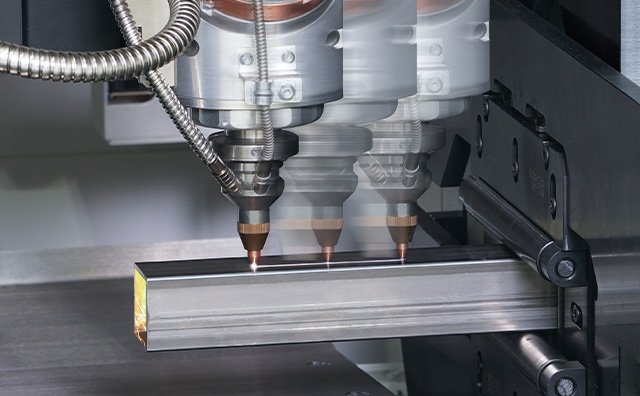
B-axis for bevel cutting as standard
The laser head with B-axis can cut materials at desired angle This ensures high-accuracy bevel cutting and improves the quality and strength of the joint.
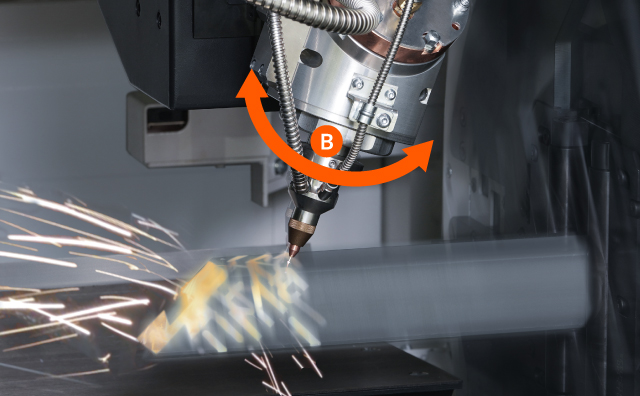
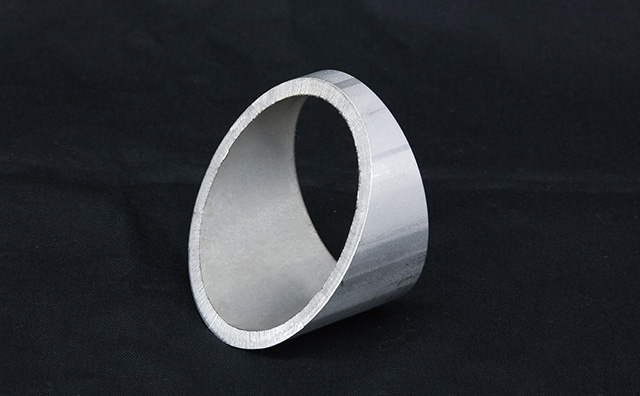
High-speed feedrate and chuck indexing speed
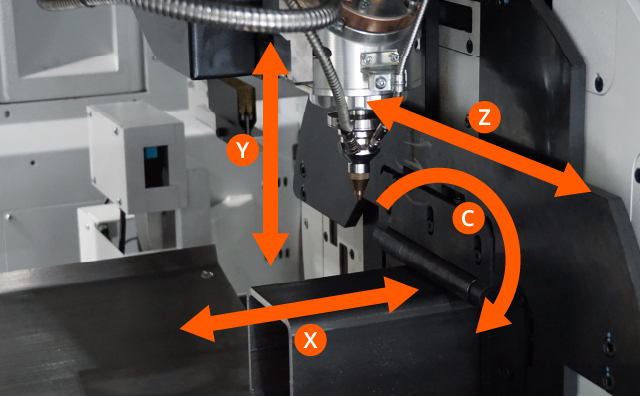
FT-150 FIBER | |
X-axis | 150 m/min |
Y-axis | 65 m/min |
Z- axis | 65 m/min |
C-axis | 54000 deg/min |
The productivity of pipe mass production operation is automated and significantly improved
By integrating the conventional pipe process, the FT-150 FIBER reduces inter-process transfers, waiting time, setup time, etc., and completes all processing on a single machine. It shortens production lead time.
Reduce in-process time of pipe processing
Conventional process
1 : Cutting with saw
2 : Punch press
3 : Deburring
4: Hole tapping
FT-150 FIBER
5: FT-150 FIBER completes all processing on a single machine
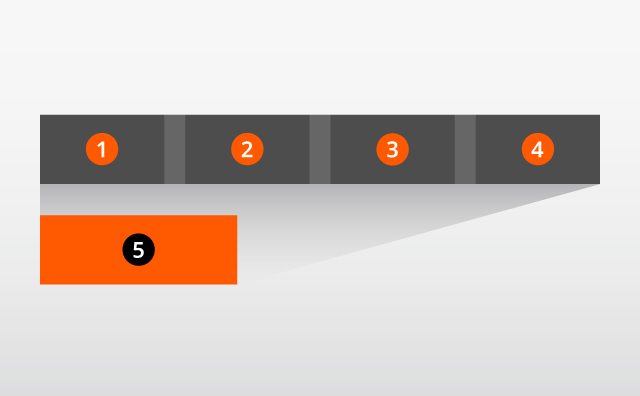
Large-capacity bundle loader for continuous operation
Materials are automatically loaded into a high-capacity bundle loader, and after laser processing, the cut parts are automatically unloaded.
Structural steel and sudden interruption workpieces can be loaded manually.
Designed for high efficiency
The loading and unloading of material is performed at the front of the machine to minimize operator movement.
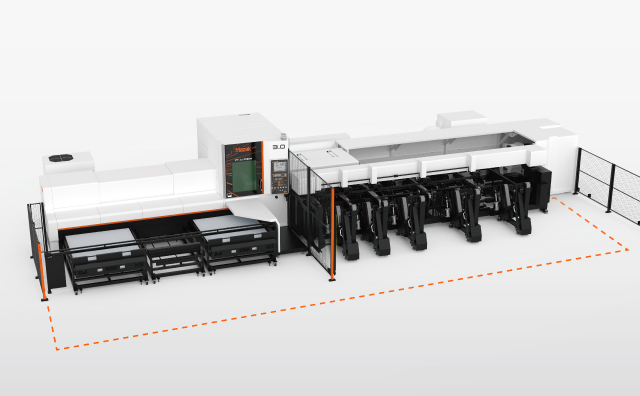
Rotary Tool Unit for drilling and tapping
Tools suitable for drilling, tapping, thermal drilling and chamfering can be attached to the optional rotary tool unit. Drill support, a supporter which hold the workpiece during drilling, is available as an option.
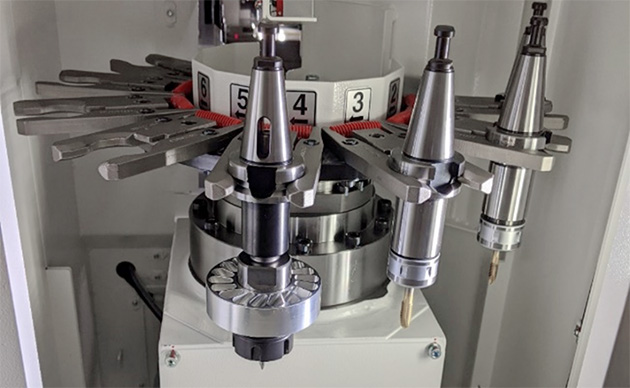
Various optional functions for high accuracy and value cutting
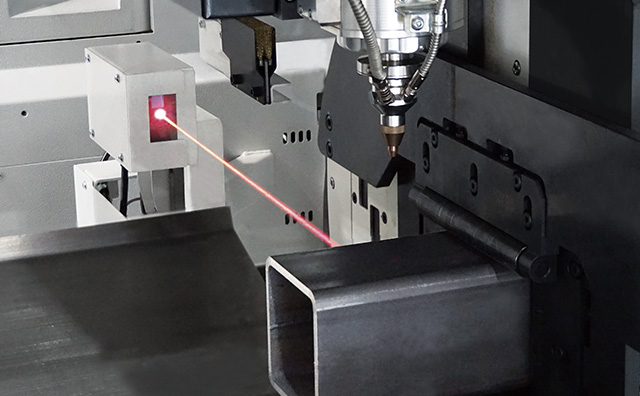
Work Center Location/Inclination Compensation
Measures the OD of pipe material and automatically compensates for material distortion to ensure high precision positioning.
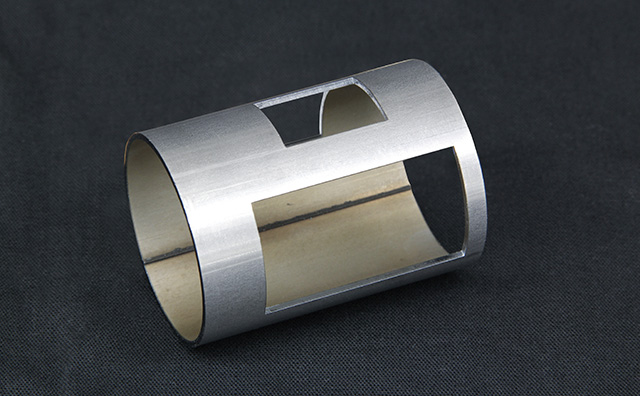
Visual Seam Locator
The weld seam of pipe material can be detected on the machine to determine the required radial position for cutting.
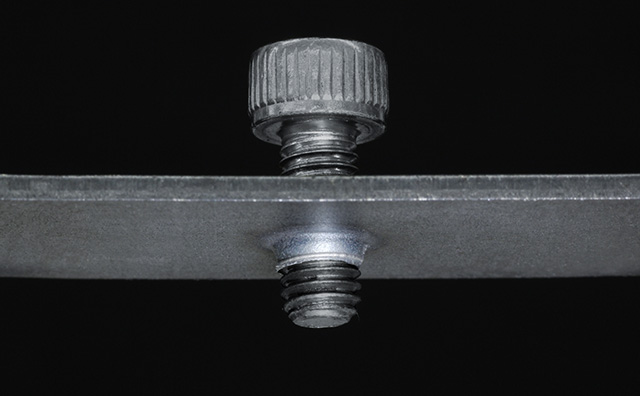
Thermal Drilling
Tapping on thin plates can be performed with the optional thermal drilling function.
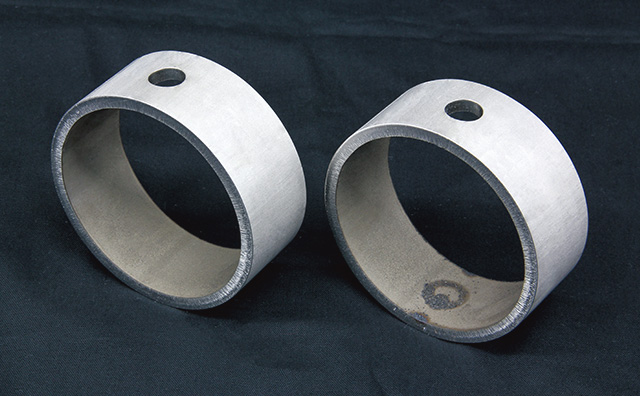
Internal Spatter Guard
The spatter guard protects the internal workpiece surface from spatters and burns, thereby preserving the quality of the workpiece.
Reduce running costs with fiber laser
The advanced technology of the fiber laser provides higher efficiency Since fiber laser processing machines do not require laser gas, they have low power consumption and are easy to maintain.
SmoothTUBE, a new CNC system for pipe processing
New graphical user interface specialized for tube processing ensures easier operation. It comes with a dual touch panel with large 21.5" screen. The flow from preparation to processing is displayed on one screen. Condition setting of scheduled operation can be changed and reprocessing can be done on the CNC system easily. The system is optionally available.
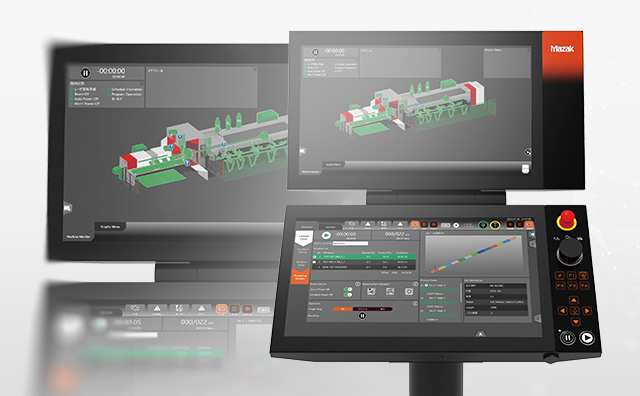